Robotic Quick-Change Technology—A Powerful Tool for Reducing Costs and Increasing Efficiency in the Automotive Industry
Robotic quick-change technology is undoubtedly a powerful tool for reducing costs and increasing efficiency in the automotive industry. In automotive manufacturing, robotic quick-change technology is widely used in fastening stations, welding stations, adhesive application stations, and more. For example, at fastening stations, robots can quickly switch between different tightening tools through quick-change devices to accommodate various bolts and tightening strategies. In welding stations, robots can swiftly change between different welding guns and clamps to meet the welding needs of different vehicle models and components. At adhesive application stations, robots can also use quick-change devices to rapidly switch between different adhesive tools, enabling automated production for various adhesive processes.
Advantages of Quick-Change Systems in the Automotive Industry:
Improved Production Efficiency:
Robotic quick-change technology can complete the changeover of different workpieces within seconds, enabling one machine to handle multiple tasks. This significantly reduces line changeover time and increases equipment utilization.
Traditional tool or fixture changes often require manual intervention, which can be time-consuming. Quick-change devices, however, can replace tools or fixtures in just a few seconds, greatly improving operational efficiency.
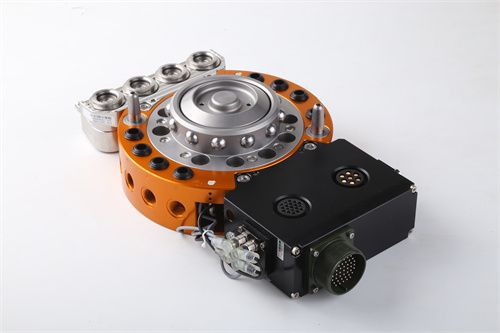
Ensured Production Precision and Quality:
Quick-change fixtures are designed and manufactured with high precision, ensuring consistent clamping force and positioning accuracy with every change. This minimizes errors caused by manual intervention or fixture wear.
This provides strong support for the precision machining of key automotive components, ensuring product quality consistency.
Reduced Production Costs:
By minimizing the labor and downtime required for fixture changes and avoiding the wear caused by frequent tool changes, companies can achieve higher production efficiency and lower operational costs while maintaining product quality.
Since a single robot can perform multiple tasks, fewer robots are needed on the production line, reducing equipment investment and maintenance costs.
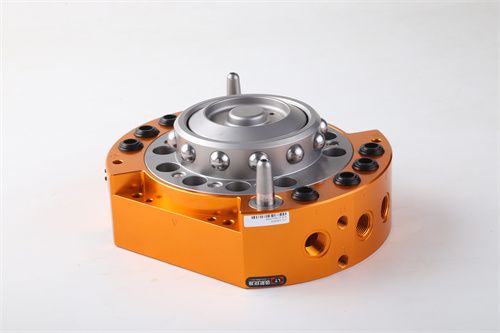
Enhanced Production Flexibility:
Robotic quick-change technology allows robots to quickly adapt to different workpieces and production demands, increasing the flexibility and adaptability of the production line.
This is critical in responding to the increasingly diverse demands of the automotive market and rapidly changing production environments.
Increased Production Safety:
By reducing the need for manual tool changes, the risk of safety incidents for operators is lowered, enhancing overall production safety.
As the automotive industry continues to evolve, the variety of tasks required on production lines is also expanding. The deep application of robotic quick-change devices provides a new approach to production. One robot can quickly switch between different end-effectors based on production needs, completing multiple tasks. This flexibility not only improves production efficiency but also reduces costs and increases safety, helping companies respond more swiftly to market changes.