Robot-driven intelligent polishing and grinding technology is becoming a core direction for future industrial upgrades.
In manufacturing sectors such as new energy storage equipment, automotive precision parts, advanced composite materials, 3C electronics, home and kitchen appliances, and high-end precision instruments, force-controlled floating grinding technology has been widely applied in key processes including grinding, polishing, mirror finishing, and deburring—significantly improving processing accuracy and production efficiency.
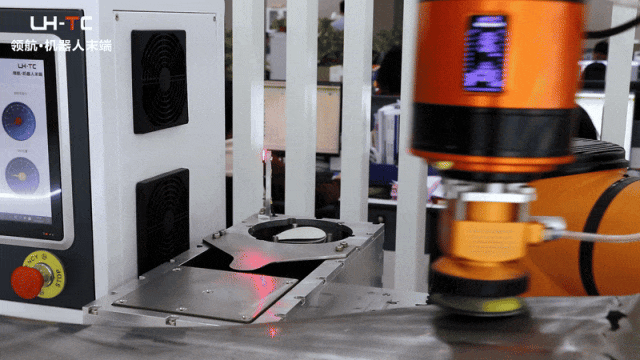
Leveraging its independently developed core technology system for “force-controlled floating grinding and deburring”, LH-TC has achieved major breakthroughs in dynamic force feedback control, floating trajectory compensation, and stable constant-force output—establishing a strong competitive edge in the smart manufacturing sector.
Taking automotive parts manufacturing as an example, LH-TC’s axial floating constant-force grinding system demonstrates innovative application in weld seam treatment. By sensing changes in the workpiece surface morphology in real time and automatically adjusting grinding pressure and floating stroke, the system ensures precise constant-force weld seam removal—effectively addressing issues such as over-grinding, under-grinding, and surface quality instability common in traditional methods.
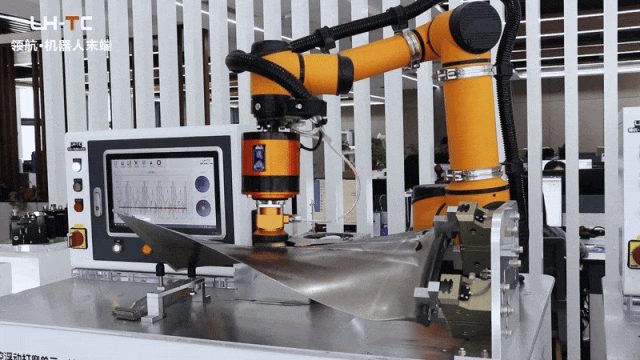
Advantages of the Axial Active Floating Constant-Force Grinding System
-
Adaptive Flexible Grinding on Complex Contours
Equipped with high-precision sensors and intelligent control systems, the grinding head adapts along surface normals to accurately deburr and chamfer complex curved surfaces.
-
Axial Active Floating Constant-Force Control
The constant-force actuator automatically recognizes posture and compensates output force with a precision within ±0.5N.
-
Visual Operation
Simple and intuitive interface, easy parameter settings, and real-time feedback of contact force data for convenient process tuning.
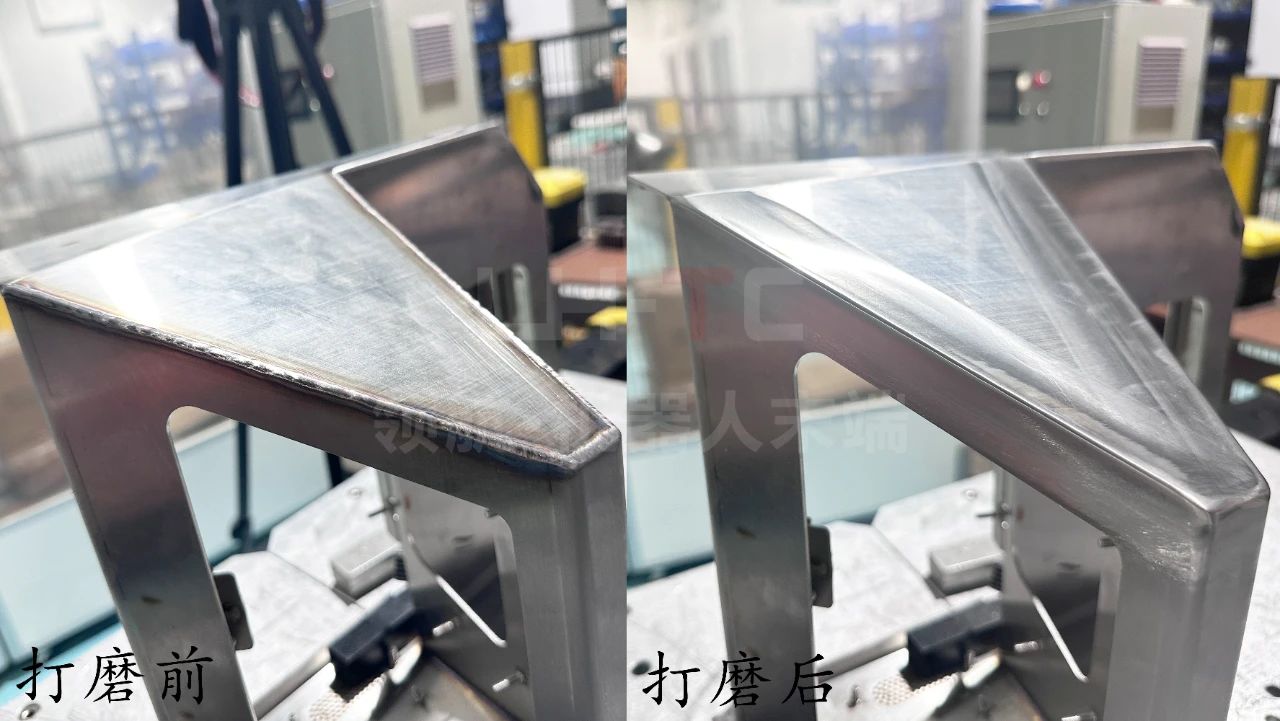
Grinding Parameters