The robotic automatic tool changer is a critical component in the field of industrial robotics, allowing robots to quickly and easily switch end-effectors (such as grippers, welding guns, spray guns, etc.) without stopping their operation. This greatly enhances the robot’s flexibility, safety, and efficiency.
Here is a detailed description of how Linghang’s automatic tool changer achieves intelligence, safety, and efficiency:
Intelligence
Automatic Identification and Calibration: Advanced tool changers are equipped with sensors and algorithms that can automatically identify and calibrate newly installed end-effectors. This reduces the need for manual intervention and improves the accuracy and speed of the replacement process.
Data Collection and Analysis: By integrating data collection systems, the tool changer can record information such as the time of each change and the usage of the end-effectors. This data can be used to analyze the efficiency of the production line and predict maintenance needs.
Intelligent Scheduling: Combined with production planning and inventory management systems, the tool changer can intelligently schedule end-effectors as needed, ensuring the continuity and efficiency of the production line.
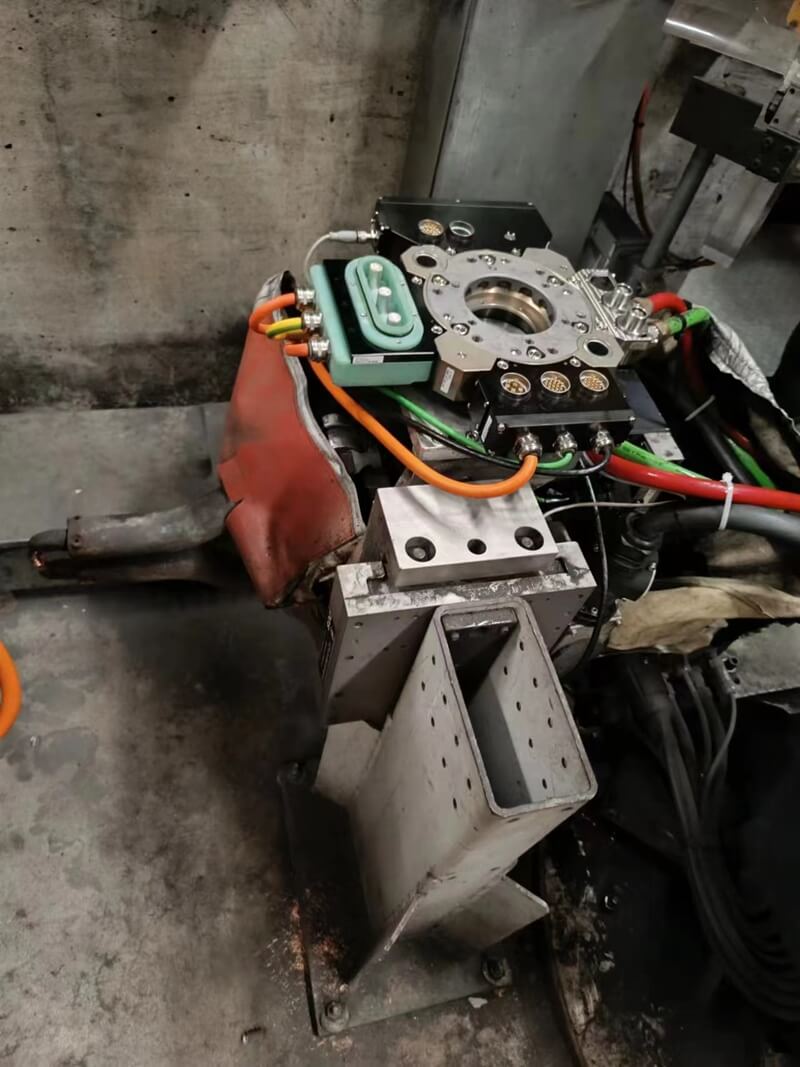
Safety
Locking Mechanism: Tool changers typically employ multiple locking mechanisms to ensure a secure and reliable connection between the end-effector and the robot during the change process. This prevents potential hazards caused by loose connections.
Safety Monitoring: Tool changers equipped with safety monitoring systems can monitor the working status in real-time. If an abnormal situation is detected (such as excessive vibration or high temperature), it can immediately trigger an alarm and stop the operation.
Personnel Protection: Through optimized design and safety procedures, the tool changer can ensure a safe distance between personnel and the robot during the changing process, reducing the risk of workplace injuries.
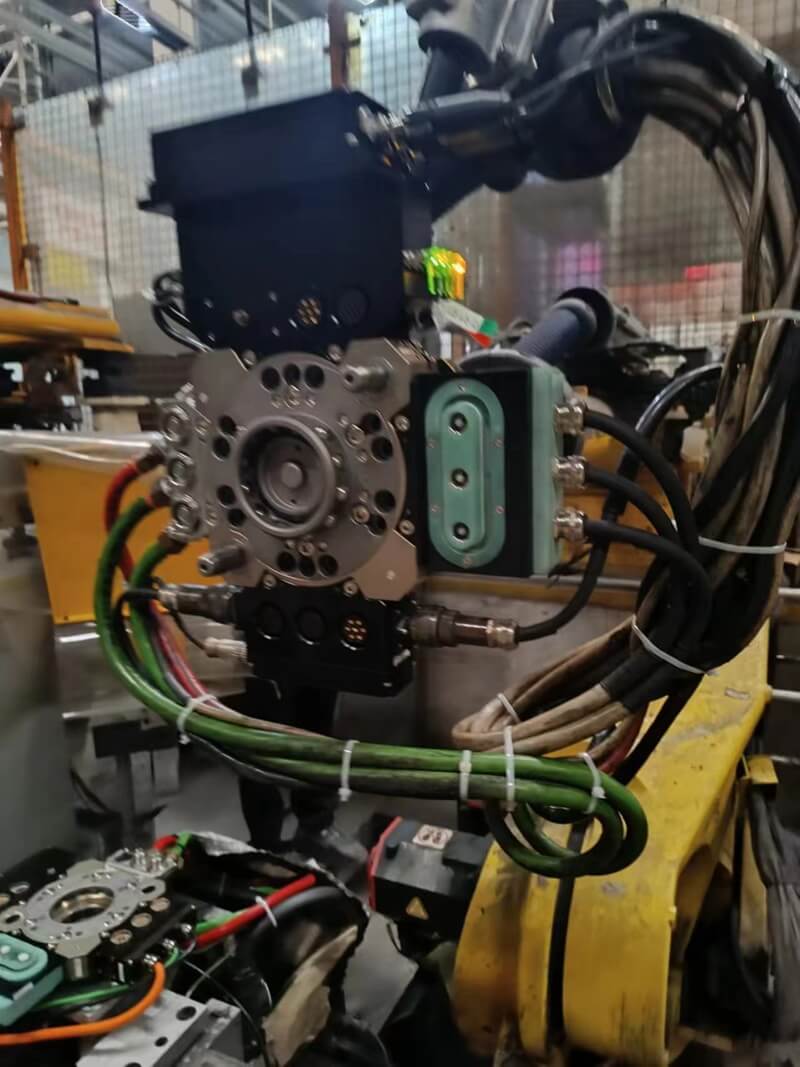
Efficiency
Quick Change: The tool changer achieves rapid end-effector replacement through optimized structure and operation processes. This reduces downtime and increases the overall efficiency of the production line.
Compatibility: Advanced tool changers support various types of end-effectors and can be compatible with different brands and models of robots. This makes the production line more flexible and capable of handling more production tasks.
Pre-programmed Functionality: Through pre-programmed functionality, the tool changer can automatically adjust the robot’s working parameters (such as speed and force) after changing the end-effector to ensure optimal production results.
In summary, the robotic automatic tool changer integrates intelligent technologies, enhances safety, and optimizes operational processes, achieving high efficiency, flexibility, and safe production for industrial robots. With continuous technological advancements and innovations, tool changers will play an increasingly important role in future intelligent manufacturing.