Currently, robots in the industrial field can be divided into three research directions: robot body, vision, and touch. They can intelligently perform tasks such as handling, palletizing, spraying, welding, and grinding. Although existing robots are becoming more intelligent and easier to use, and have relatively complete vision systems, in terms of the current status of robots in China, their competitiveness in high-end fields is weak, and there is still much room and challenges for intelligent upgrades.
In the field of grinding, there are three technical routes: First, traditional manual polishing, which produces a large amount of dust during workshop polishing, seriously endangering workers’ health. The quality of manually polished products is uneven, and the output is very low. Second, robotic rigid grinding, which has a high threshold for robot debugging, low operational efficiency, and mainly relies on engineers’ experience, resulting in low grinding output and high overall costs. Hard grinding also affects the robot’s lifespan in the long term. Third, robotic system-controlled grinding paths, where the force control system controls the grinding intensity, can adapt to any form and any weight of grinding tools, offering high grinding efficiency and the highest product output.
Force-controlled floating grinding tools enable robots to sensitively control contact with curved surfaces. An independent control system, not relying on any robot, can adapt to any type of grinding tool and has a fast response speed. Compared with existing grinding technology routes, active compliant force control technology and surface treatment systems have the following advantages:
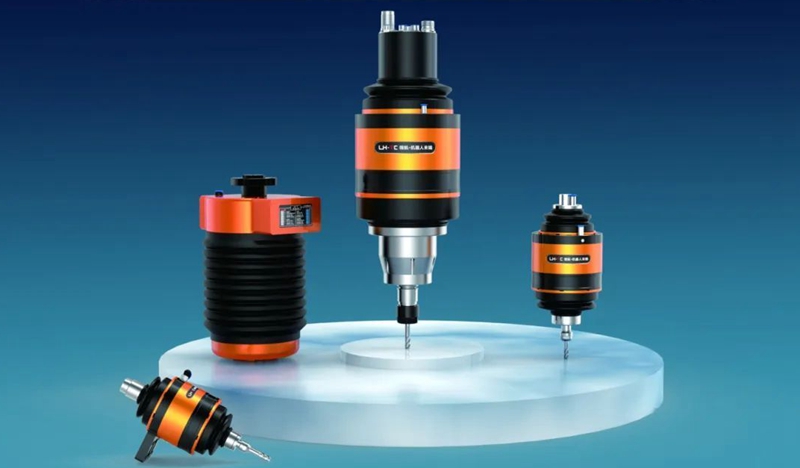
01 Efficiency Improvement
Efficiency improvement: Ready to use; any robot can have flexible force control functions, achieving fine grinding operations; process software quickly imports models to generate paths. Reduces robot selection cost by over 100,000 yuan.
02 Quality Improvement
Quality improvement: Intelligent force control with built-in workpiece error compensation improves the workpiece grinding rate by 20%.
03 Cost Reduction
Cost reduction: Isolates impact force generated by grinding contact, protecting the robot body and saving 70% of debugging time cost.
The force-controlled floating grinding tool integrates sensing, control, and execution systems structurally. It can perform gravity compensation on the end tool as needed and accurately output contact force parallel to the robotic arm axis. Additionally, this tool can adapt and retract based on the corridor characteristics of the contact surface, solving the automation issue between sensitive contact surface processes and rapid contact movements. It is widely used in robotic polishing, grinding, deburring, weld seam removal, chamfering, and other surface treatment processes. The force-controlled floating grinding tool has strong adaptability to grinding scenarios, fast deployment speed, and minimizes maintenance costs and cost performance, meeting customers’ needs for personalized custom development.
The force-controlled floating grinding tool is mainly used for surface polishing of workpieces, deburring edges, weld seam polishing, internal cavity and hole deburring, and hole thread processing. It is applicable in industries such as soft material polishing (plastic rubber, car tail plates, putty polishing, composite materials), metal hardware polishing (metal cabinets, cast iron shells, cast steel parts, cast copper parts), medical equipment grinding (medical MRI equipment, internal medicine instruments, ECG machines), optical lens grinding (acrylic lenses, plexiglass lenses, concave-convex lenses), and more.